Technical Intro
We are at the forefront of hyperscale data centre construction, and continuously push ourselves to improve on very aspect of delivery. Greater focus is being placed on new approaches, creating more value for our clients to develop and construct our projects safer, faster, more efficiently and lowering the overall cost. Working with Mace you get not just a construction contractor, you get a delivery partner.
DfSMA
We consistently look to develop innovative techniques and drive value through innovation and DfSMA across every project. By challenging the way the buildings are designed and constructed to deliver faster and to higher level of quality.
Innovation and DfSMA is embedded in our culture – both in our processes and in how we think, communicate and engage with our clients. Greater focus is being placed on new approaches to creating more value for our clients to develop and construct our projects safer, faster, more efficiently and lowering the overall cost. Such a keen eye for innovation revolutionises how we think and behave on a daily basis, in turn making us a more productive business and delivering greater value.
A significant example of this was the development of a unique approach to fitting out the data hall with the goal of avoiding the risks and delays that come with working at height, which was required for a serious bulk of the work. Mace use a modularised approach that offers ‘lift and connect’ capability. The pre-fabricated module is safely and efficiently assembled off-site and then transported to the data centre where it can be put in by a specialist crane. By putting the module together on an assembly line the Mace team significantly reduced the need to work at height.
When developing the new approach, Mace conducted a series of studies on the current sequence to fully understand the inefficiencies. We found that it takes approximately 9000 hours for an electrician to complete their work on each data hall, and that 25-30% of an electrician’s time was spent as a MEWP “spotter” - time that could be spent much more effectively. In addition, around 50 MEWPs are used on site which can cause damage to floors and walls as they move around, they can also put workers on the floor at risk. Finding a solution was made more difficult by lifting complications and intellectual property rights. However, the final modularised solution was eventually found and has brought many benefits to Mace most importantly, making the working environment much safer for staff on the site.
BIM
Our sites are currently viewed as the leading projects for BIM innovation and implementation within Mace. By using BIM initiatives across the entire scope of delivery we have improved accuracy and delivered more efficiently.
Implementing a new way of working relies on a philosophy of project team communication and collaboration. The Mace BIM team drive the philosophy and management of BIM on site, setting out the rules early in the project phase, concentrating on two key goals, model management - with emphasis on tying into the design review process and construction programme, and field management -with emphasis on using the data we collect in the field, to improve management to achieve the aggressive project milestones.
The BIM innovations have had tangible results improving consistency across the entire scope of delivery:
• Our live dashboard enables the project team to have real time information advising which QAQC checklists are complete/incomplete, what equipment has been commissioned and any outstanding snags/defects. This has focused our team on works that require immediate attention which in turn has resulted in successful project milestone completion.
• The BIM, planning and construction teams have collaborated to produce a critical path programme. This programme is tailored to our BIM coordination works, highlighting when locations require BIM freeze dates.
• Laser scanning has improved our project quality. The volume of out of tolerance works has dramatically decreased throughout the project duration, avoiding on site re-work and streamlining project delivery.
• The BIM hubs have improved efficiencies on site, by providing an easily accessible space for all contractors to view and check drawings it has saved time and improved accuracy of delivery as all project information is available in the field.
• BIM360 Field has given our management a tool to complete all necessary QAQC checks on site and empowers them with real time live data and access to the current design set at all times.
Our use of BIM is constantly improving and changing as we adopt new initiatives to deliver industry-leading projects for our clients.
Commissioning
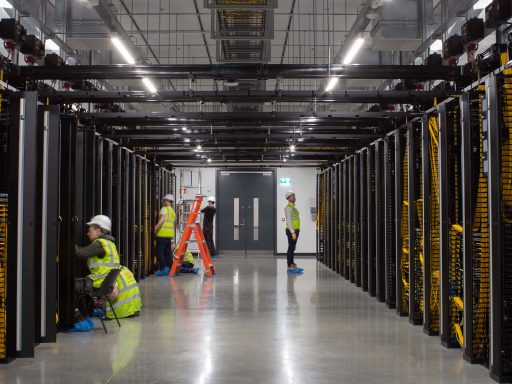
We have refined the complex commissioning and QA/QC processes into lean digital workflows and successfully integrated BIM into project delivery using Autodesk’s BIM 360 ‘Field’ Platform.
The team have created automated processes using Application Programme Interface (API’s) to allow different platforms to automatically synchronise together. BIM 360 Field collects a large amount of data daily which can be customized to suit exactly what our client wants to track.
Autodesk BIM 360 Field is used by all site teams for commissioning scripts and QA/QC checklists. All equipment on site which is required to be recorded and tracked receives a QR Code. This allows site users to update information live on site every hour of every day. The system provides the project team with the functionality to electronically record information such as progress monitoring (deliveries, installations, QA/QC, commissioning achieved dates etc.) and the ability to capture information on site for the recording of defect and snagging issues.
As each piece of equipment is tagged at Factory Witness Test (FWT), it means that at the end of the project, the client can scan any piece of equipment on site, and immediately have every piece of information attached (from FWT documentation and images, warranty dates, as-built drawings, training manuals, O&M information etc).
Equipment on the project is tracked in line with the different stages of tagging for commissioning. As all this information is now digitalized, it also means that it can now provide the basis for data analysis for reports and graphs which can give the project team high level overviews of progress and roadblocks.
To supplement the use of both BIM 360 Field and Cx Tagging process, and to enable us to obtain outputs of status and forecasting, Live Tracking documents were developed that obtained the native data from within BIM 360, Conject and other platforms in use on the project, to provide progress status and forecast reporting based against programme milestone dates. These were a huge success in giving accurate and granular visibility on install and commissioning progress against each individual piece of equipment or system with their forecast capabilities providing early warnings of any possible delay so we could mitigate it.
Quality
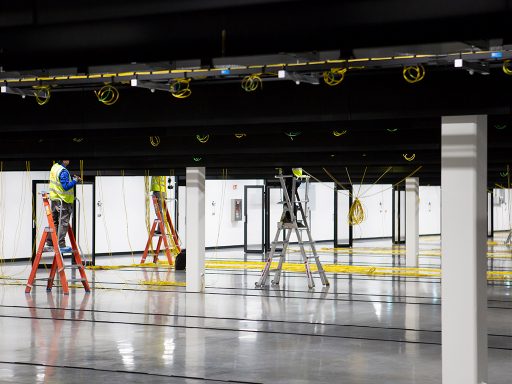
All Mace projects are delivered in line with our Service Excellence initiative. This monitors and standardises our top quality service across all aspects of delivery to meet and exceed our Clients expectations.
Quality best practice is promoted and rewarded. All new starters attend a site specific Quality Induction which includes a video filmed on site and is supported by our ‘4 Steps to Quality’ campaign. There are rewards for Quality Contractor of the month and individuals for demonstrating Quality Best Practice. A major recent achievement was the handover of a project with zero defects and all turnover documentation issued to the client in advance of the deadline. We believe the legacy of every project should not only be a Quality Benchmark for our client, but for data centre construction worldwide.